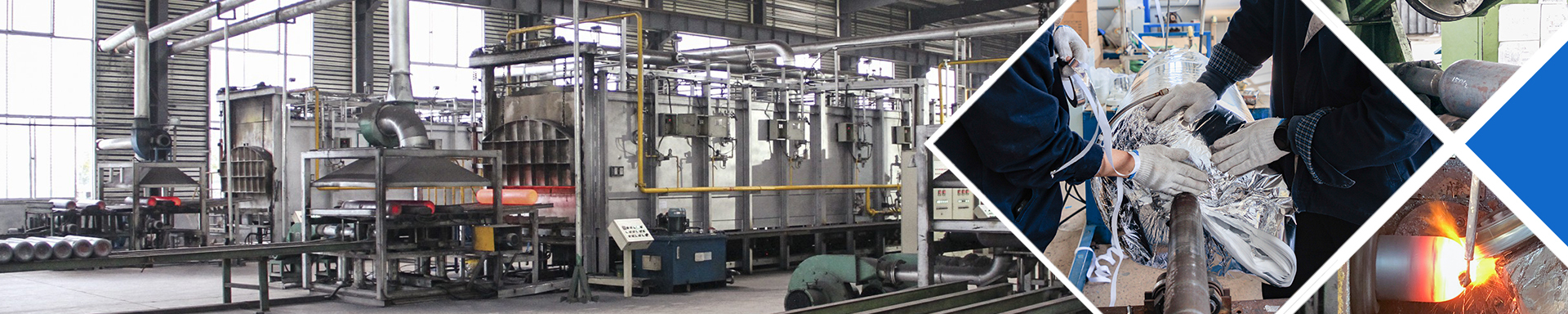
Aplikasi dan Persyaratan Tabung Gas Obat
2024-02-13 11:05memerlukan audit berkala oleh perusahaan gas dan otoritas yang berwenang untuk memastikan kepatuhan terhadap otoritas manufaktur dan pemasaran
Denganasi.
Since the late 1800s many millions of people have relied upon medicinal gases being supplied to them from gas cylinders. These gases are used for a wide range of procedures and modern healthcare systems could not survive without the safe delivery every day of medicinal gases, in particular medicinal oxygen from thousands of gas cylinders.
Medicinal gases supplied in high pressure gas cylinders have an excellent patient safety record and this publication demonstrates the intrinsic safety of the delivered package as well as the processes and procedures undertaken to ensure the safety of the delivered product. The publication considers a number of areas including how medicinal gases have evolved and how the gas cylinder package has developed into a technically advanced item of equipment. Section 7 describes a study conducted by EIGA Members on the delivered quality of medical oxygen. Section 6 indicates there is no evidence of safety concerns regarding patients receiving medicinal oxygen.
2.History of medicinal gases
The predominant medicinal gas used by patients is oxygen. This is almost exclusively produced in air separation plants, usually referred to as ASUs.The earliest recorded use of oxygen in medicinal applications was at the end of the nineteenth century. Production of oxygen was not widespread and so the opportunity to obtain the gas was limited, though the benefits of using oxygen were immediately appreciated by medical practitioners. As production of oxygen for industrial processes developed, so did availability of oxygen for use in medical applications. The use was linked to the development of high pressure gas cylinders that could store sufficient quantities of the gas and be economic to transport. Several other technologies contributed to this increasing use of oxygen, such as the inventions of flexible tubing and the face mask.
The benefits of oxygen therapy became apparent during the first world war to treat the effects of poison gas. From 1918 onwards, the increased production of low cost oxygen ensured that oxygen therapy could be provided on a wide scale.
As the industrial gases industry has progressed to higher pressures, lighter cylinders and improved delivery systems, these benefits continue to be made available to the users of medicinal gases.
It should be noted that medicinal gases, including their packaging, are subject to the same authorization processes as other medicinal products, thus requiring the same modules for the container closure system. In the case of medicinal gases these container closure systems are the cylinders and valves.l The approval of the different types of cylinders and valves covered in this publication are therefore a significant part of the authorization process for medicinal gases.
3.Types of gas cylinder package
The package used to distribute compressed medicinal gases consists of primarily of two parts; the cylinder and the cylinder valve. To facilitate the safe delivery of compressed gases in cylinders, other accessories can be used such as regulators and flow meters. Examples of typical gas cylinder packages in common use are shown in Figures 1, 2 and 3.
3.1Gas cylinders
Today, most high pressure gas cylinders in medicinal gas service are of seamless steel construction, and are filled to a working pressure up to 200 bar.
These steel cylinders are constructed to European, International or local Standard, for example EN 1964. Transportable gas cylinders. Specification for the design and construction of refillable transportable seamless steel gas cylinders of water capacities from 0,5 litre up to and including 150 litre. Cylinders made of seamless steel with an Rm value of less than 1100 MPa and ISO 9809-1 Gas cylinders-Refillable seamless steel gas cylinders-Design, construction and testing-Part 1: Quenched and tempered steel cylinders with tensile strength less than 1100 MPa, 1. These standards have undergone a rigorous development process by international standards organizations, such as CEN and ISO with participation by many EIGA members or Local standard, cylinder manufacturers and other stake holders. The steels used for the manufacture of gas cylinders are advanced alloys. Before these cylinders can be placed on the market within the European Union, they are subjected to rigorous approvals as required by legislation such as Directive 2010/35/EU on transportable pressure equipment (TPED)
In addition to steel gas cylinders there are also aluminium alloy gas cylinders in use developed and approved through a similar process as steel cylinders.With technical advances, the suppliers of medicinal gases are increasingly looking to cylinders of a composite construction. These composite cylinders have a metal liner that is over wrapped with a fibre, such as carbon fibre.
3.2Gas cylinder valves
The gas cylinder valve is the interface between the user and the delivered product and EIGA Members have expended considerable effort to ensure that this interface both satisfies all technical requirements as well as assisting the user in the delivery of the product. All valves are required by legislation to be type approved by competent authorities, based on requirements that include:
Transportable Pressure Equipment Directive ;EN ISO 10297, Gas cylinders. Cylinder valves. Specification and type testing ;EN ISO 10524-3, Pressure regulators for use with medical gases. Pressure regulators integrated with cylinder valves ;EN ISO 15996, Gas cylinders. Residual pressure valves. General requirements and type testing .There are a number of different types of cylinder valves in use, and these are summarized below.
3.2.1 Standard gas cylinder valves
The basic gas cylinder valve is usually referred to as an O-ring valve. The name refers to the sealing mechanism which is an O ring located on the valve spindle that ensure leak tightness of the valve. There are many millions of these types of valves in service around the world and they are renowned for their reliability.
3.2.2 Residual pressure valves
In addition to the standard gas cylinder valve more and more residual pressure valves (RPV) are being put into service. Residual pressure valve can be with or without Non return function This type of valve adds an additional function to the standard valve by having a device that prevents impurities such as moisture and other contaminants entering the cylinder during use.
3.2.3 Valves with integrated pressure regulator (VIPR)
Beside the RPV, more sophisticated valves with an integrated pressure regulator (VIPR) are in use. This type of valve has not only a residual pressure function but delivers the medicinal oxygen at the required pressure and gas flow to the patient. VIPRs also prevent the back flow contamination.
4.Filling of gases into gas cylinders
Oxygen is produced from cryogenic distillation in air separation plants. These plants take atmospheric air and compress, purify and expand the air to liquefy it to cryogenic temperatures. Oxygen is then distilled from the liquid air. For medicinal gases produced in air separation plants there is a requirement for manufacturing authorization for the production process.
The cryogenic liquid product is distributed to a specialist cylinder filling facility where the product is filled into gas cylinders as a compressed gas.
The production/filling process of medicinal gases into cylinders have numerous controls and checkpoints that include:
l Cylinder charging pressure is appropriate for the cylinder and valve combination;
l Cylinders and valves are within periodic inspection period;
l Confirmation that valves are suitable for the gas service;
l Verification there is a positive residual pressure inside the cylinders;
l Cylinder bodies, where appropriate, have been painted according to the applicable standards and guidelines; and
l Cylinders and valves are clean and not damaged;
Once the pre-filling inspection have been completed, the cylinders are connected to the filling system. Cylinders are usually filled in batches. During filling the valves are examined and verified to be free from leaks. At the end of filling new batch labels are attached to the cylinders.Depending of the batch size one or more cylinders are analyse for the quality of the gas, to confirm that the batch is in accordance with the specifications in the monographs in the Local Pharmacopeia. All test results are recorded in a batch journal/batch report, and the batch is certified and released by the qualified person.These production, filling, analysis and release processes have been through a validation process where all steps are checked and validated before production is authorized, Consequently, these steps are carried out according to the requirements of the Good Manufacturing Practice.The above processes are subject to periodic audits by both gas companies and competent authorities to ensure compliance to the manufacturing and marketing authorizations.